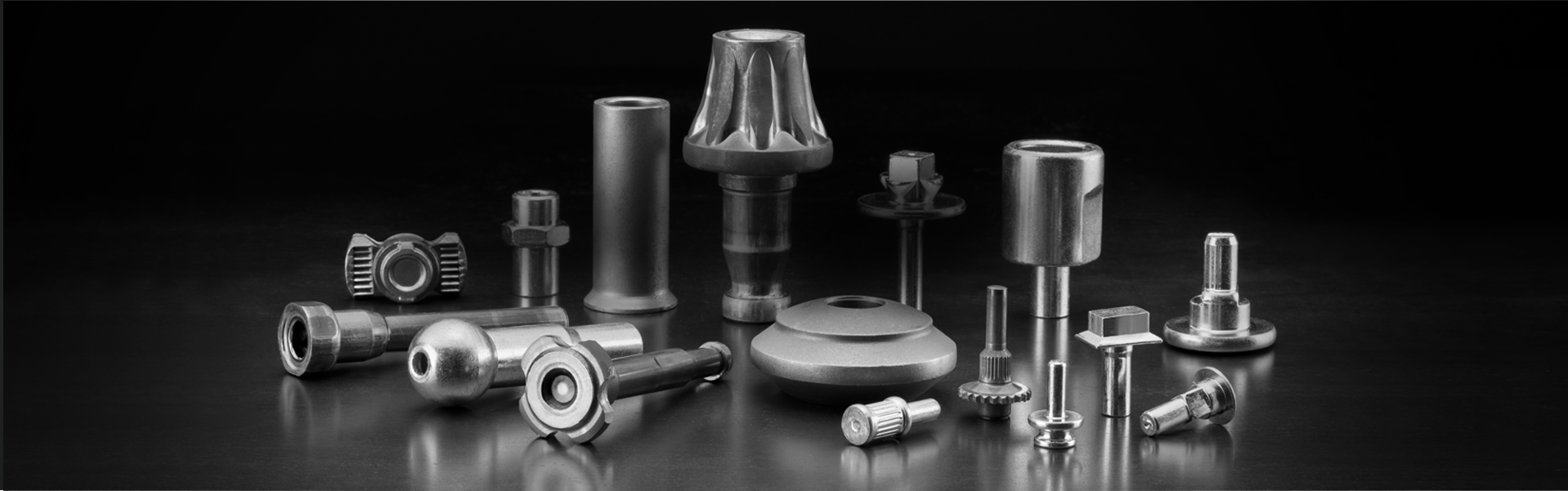
Extursion dies
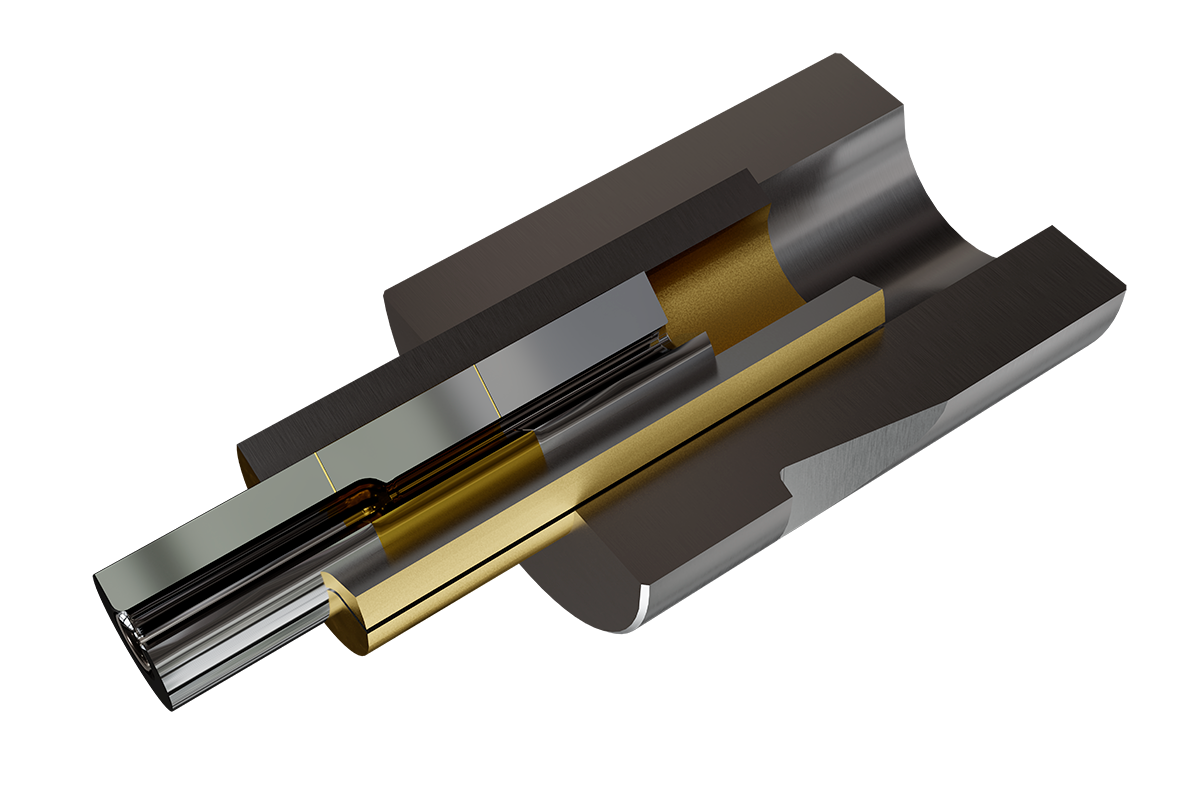
Over the past 25 years TEMSA has developed its own state-of-the-art technology in order to improve tools’ lifespan whilst keeping costs down.
This die design technology allows the use of interchangeable carbide nibs and a PVD-TiN coating on the working area. On extrusion dies, a well-polished surface is essential: At TEMSA, the mirror polishing is done before and after PVD coating. This grants a better flow of the material, extending the tool’s lifespan and preventig the die from seizing-up.
Closed extrusion dies are used when more than 30% cross-section
reduction is needed.






